● Industrie
Machines à vapeur
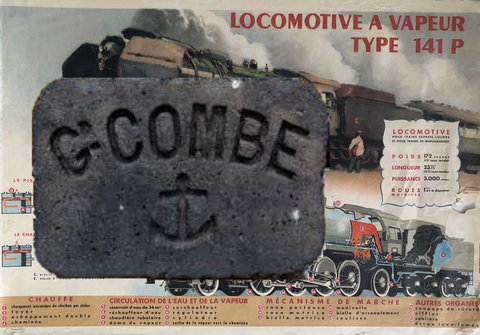
La machine à vapeur est une invention dont les évolutions les plus significatives datent du XVIII° siècle. C'est un moteur à combustion externe qui transforme en énergie mécanique, l'énergie thermique de la vapeur d'eau, produite par une chaudière au charbon.
Ce charbon, nécéssaire au chauffage de la chaudiére, est fourni sous format de briquettes (ou de boulets).
Du charbon pulvérisé est en suspension dans un bac de décantation. Après séchage à haute température (100°), mélange avec du brai en poudre et passage dans des presses hydrauliques pour donner ces briquettes (ou des boulets).
L’ancre présente sur la briquettes de LA GRAND'COMBE rappelle que les premiers usages ont été destinés à la MARINE.
Centrales Thermiques
La nécessité de réduire les impacts sur l’environnement conduit à rechercher l’amélioration du rendement des centrales les rejets étant inversement proportionnels au rendement. Certaines nouvelles technologies sont déjà en œuvre, d’autres ne sont qu’au stade de pilotage:
- Centrales sub-critique à injection:
- Les centrales PCI à co-génération:
- Les centrales PCI super-critiques:
- Les lits fluidisés atmosphériques:
- Les lits fluidisés pressurisés:
- Gazéification:
Les IGCC paraissent bien être une solution d’avenir en raison de leur aptitude à brûler tout type de combustible et de leur plus faible rejet de polluants, mais de gros problèmes technologiques restent à résoudre (corrosion des turbines en particulier).
Fonderies
La fonte est le métal recueilli après la fusion du minerai dans le haut fourneau. C'est un alliage de fer et de carbone (plus de 2,5% de carbone). L'affinage est la transformation de la fonte en acier (moins de 1,8% de carbone par réduction du taux de carbone dans l'alliage. La méthode utilisée alors était le martelage des barres de métal, qui peu à peu, réduisait le pourcentage carbone.
Le fourneau qui servait à transformer le minerai en fonte s'appelait un "Haut Fourneau" parce qu'il était rempli par le haut, celui qui servait à couler la fonte en barres pour sa transformation en acier ou en articles en fonte sophistiqués, s'appelait un "Fourneau à Marchandise", ou cubilot... Le bois servit longtemps de combustible dans les "Bas Fourneaux", pour les fonderies et les forges, mais on s'aperçut assez vite que le charbon de bois chauffait plus fort...[chouannerie]
Le charbon de bois devint extrêmement coûteux ... et Abraham DARBY tenta de développer la coulée au coke: pour réduire le minerai de fer et le carburer dans le haut-fourneau afin d'obtenir la fonte, il utilise le coke, graphite (carbone) très pur, obtenu par distillation de la houille dans un four.[Wikipedia]
L'industrie sidérurgique est un important consommateur de charbon: la production d'une tonne d'acier exige environ 600 kg de charbon à coke. Il est obtenu à partir d'un traitement thermique du charbon.(carbonisation). Ce traitement se fait à l'abri de l'air dans les « fours à coke ». On élimine les matières volatiles du charbon et cette dévolatilisation laisse un produit solide, fissuré et mécaniquement résistant : le coke. Il est constitué uniquement de carbone et de matières minérales calcinées. [Charbonnages De France]
Enfin, au pied du serre de DURET, au bout du pont du Marché d'ALAIS, sur la rive droite du Gardon, il existe quatre fours à chaux alimentés par l'étage oxfordien supérieur. L'extraction du calcaire a lieu à côté des fours; la pierre se cuit à la houille.
Aussi fabrique-t-on, dans ces fours, de la chaux grasse ou maigre, à volonté, suivant qu'on emploie les couches de calcaire pur ou les couches de calcaire gris argileux qui forment la base dela montagne.
Ces fours sont chauffés avec la houille d'ALAIS.
Pour cuire 1.100kg de calcaire, propre à faire de la chaux grasse, il faut 175kg de combustible, ce qui produit 500kg de chaux. Cette opération dure environ 48heures.
Pour cuire 1.000kg de calcaire argileux, pour chaux maigre, il faut 125kg de houille, ce qui donne 500kg de chaux. Cette cuisson dure 30 heures environ.
[Dumas]